Superbike to super-naked | How Honda tweaked the 2017 Fireblade engine for the 2025 CB1000 Hornet
Reusing Superbike Engines: A Tale of Two Eras
The practice of transplanting superbike engines into naked bike chassis has been a popular strategy for achieving high-performance roadsters. A prime example is Honda's original CB900F Hornet, launched in 2002, which successfully harnessed the power of the 919cc FireBlade engine. However, the advent of stringent modern emissions regulations has significantly altered the landscape.
Modern Emissions Challenges
- Stricter Standards: Current Euro 5 and US EPA emissions standards are significantly more demanding than their predecessors, requiring manufacturers to implement advanced exhaust gas treatment systems like catalytic converters and oxygen sensors.
- Engine Modifications: Adapting a superbike engine designed for a specific application (like a race track) to meet these stringent standards often requires significant modifications to the engine's internal components, exhaust system, and engine management system.
- Cost Implications: These modifications can be expensive, hindering the economic viability of such transplants for manufacturers.
Key Takeaways
- Reusing superbike engines for naked bikes is a viable strategy for achieving high performance but faces significant challenges in the modern era.
- The primary obstacle is the implementation of modern emissions regulations, which require costly modifications to engine systems.
- The economic feasibility of this approach is a key concern for manufacturers, as it can significantly impact the overall cost of the vehicle.
Practical Implications
- Increased Development Costs: Manufacturers must invest in extensive research and development to ensure that re-purposed engines meet stringent emissions standards and perform adequately.
- Limited Market Appeal: The higher cost associated with emissions compliance may limit the appeal of such models to a niche market of performance-oriented enthusiasts.
- Alternative Solutions: Manufacturers are increasingly turning to purpose-built naked bike engines that are designed from the ground up to meet emissions regulations while delivering robust performance.
Comparison with Similar Technologies
- Purpose-Built Naked Bike Engines: Manufacturers like Yamaha (MT-09) and Kawasaki (Z900) have successfully developed powerful naked bike engines that are specifically designed to meet emissions regulations while providing strong performance characteristics.
- Electric Powertrains: The rise of electric motorcycles offers an alternative approach to high-performance riding, circumventing the complexities of emissions regulations altogether.
Honda's engine adaptation
Adapting to Euro 5+ Emissions Standards
Honda's approach to meeting the stringent Euro 5+ emissions regulations for gasoline engines is a testament to their commitment to innovation and environmental responsibility.
Key Components of the Solution
- Engine Optimization: Honda has refined their engine designs to maximize fuel efficiency and reduce emissions. This involves optimizing combustion parameters, including spark timing, air-fuel ratios, and engine mapping.
-
Advanced Exhaust Aftertreatment Systems: The exhaust system plays a crucial role in reducing harmful pollutants. Honda utilizes a multi-stage system that includes:
- Catalytic Converters: Convert harmful gases like carbon monoxide (CO) and hydrocarbons (HC) into less harmful substances.
- Diesel Oxidation Catalysts (DOCs): Oxidize particulate matter (PM) and other pollutants.
- Selective Catalytic Reduction (SCR): Reduces NOx emissions using a urea-based solution.
- Lean-Burn Technology: Honda's engines operate with a lean air-fuel mixture, which improves fuel efficiency and reduces CO emissions.
- Variable Valve Timing and Lift (VTEC): This technology optimizes valve timing and lift for improved efficiency at various engine speeds.
Practical Implications
These adjustments ensure Honda vehicles comply with the latest environmental regulations while maintaining strong performance and fuel economy.
Comparison with Other Technologies
Honda's approach to Euro 5+ compliance is comparable to other manufacturers using similar technologies. However, Honda's focus on optimizing existing engines, rather than introducing entirely new designs, demonstrates their commitment to sustainability and cost-effectiveness.
Important Notes
- The specific technologies and configurations used may vary depending on the engine size and vehicle model.
- Meeting Euro 5+ standards requires ongoing development and refinement of engine and exhaust systems.
- Honda's continued innovation ensures their vehicles remain competitive and environmentally responsible in the evolving automotive landscape.
The 2017 Fireblade's engine
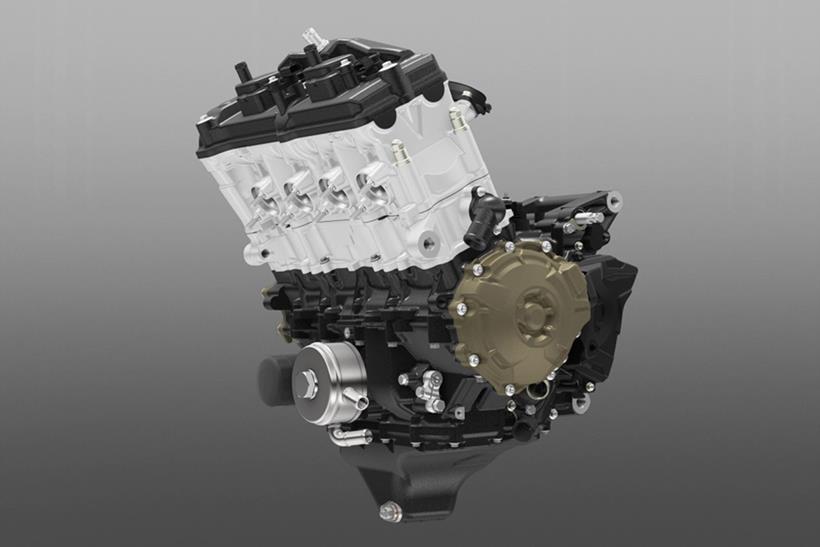
The Honda CBR1000RR Fireblade: A Leap Forward in 2017
The 2017 Honda CBR1000RR Fireblade, codenamed SC77, represented a significant evolution for the iconic sportbike. This iteration marked a substantial increase in power output, while simultaneously meeting the stringent Euro4 emissions standards, a testament to Honda's engineering prowess.
Power Gains and Emissions Compliance
- Power Bump: The SC77 boasted a peak power output of 189bhp, a significant increase over its predecessor's 168bhp. This jump was achieved through a combination of engine refinements, including a revised intake and exhaust system, optimized camshaft profiles, and revised ECU mapping.
- Euro4 Compliance: The Fireblade's new engine design also ensured compliance with the stringent Euro4 emissions regulations, demonstrating Honda's commitment to both performance and environmental responsibility.
Key Takeaways
- The 2017 Fireblade marked a notable advancement in power and emissions compliance.
- The SC77 model showcased Honda's ability to balance performance and environmental considerations.
"The new Fireblade is a real step forward, offering more power and improved handling, without compromising on its iconic character." - Honda press release
This power surge, coupled with the refined chassis and electronic rider aids, solidified the Fireblade's position as a dominant force in the superbike class. Its performance on the track and on the road, combined with its refined aesthetics, made it a highly sought-after machine. The SC77 Fireblade pushed the boundaries of what a modern sportbike could achieve, setting the stage for future advancements in the world of motorcycles.
The 2017 Honda Fireblade's engine
Honda CB1000 Hornet Engine: A Focus on Efficiency
While the Honda CB1000 Hornet's engine might not boast the eye-popping peak power of some rivals, its modest approach to design is a key factor in its exceptional performance and suitability for the new Hornet platform.
Technical Specifications:
- Displacement: 999cc
- Engine Type: Inline 4-cylinder, liquid-cooled
- Power: 121 bhp at 9,250 rpm
- Torque: 99 Nm at 7,250 rpm
Key Takeaways:
- Efficiency over Power: The Honda CB1000 Hornet's engine prioritizes smooth power delivery and rideability over raw peak power figures. This approach translates to a more enjoyable and manageable experience for everyday riding.
- Lightweight Design: The engine's compact size and lightweight construction contribute to the Hornet's agile handling and responsiveness. This translates to a fun and engaging riding experience, especially in city environments.
Real-World Applications:
The Hornet's well-balanced engine characteristics make it ideal for a wide range of riding scenarios. From navigating city traffic to enjoying spirited backroad blasts, the engine's smooth power delivery and responsive throttle contribute to a consistently enjoyable experience.
Comparison with Competitors:
While competitors might offer higher peak horsepower, the Honda CB1000 Hornet's engine stands out with its superior rideability and efficiency. The Hornet's focus on smooth power delivery and a user-friendly experience makes it a strong contender for riders who prioritize practicality and a well-rounded package.
Euro4 and Euro5 emissions regulations
The Euro 4 Emissions Standards: A Significant Shift
The adoption of the Euro 4 emissions standards marked a major departure from the previous Euro 3 regulations, significantly impacting the design and performance of internal combustion engines. This shift was driven by the need to curtail harmful pollutants and improve air quality.
Key Changes in Euro 4:
- Reduced Emissions Limits: Euro 4 drastically lowered limits for carbon monoxide (CO) and hydrocarbons (HC) by over 50% compared to Euro 3.
- Enhanced Testing Procedures: More stringent testing methods were implemented, including real driving emissions (RDE) testing, which evaluates emissions under real-world driving conditions.
Practical Implications for Engine Design:
The stricter Euro 4 regulations forced manufacturers to adopt new technologies and design strategies for their engines. These include:
- Advanced Fuel Injection Systems: More precise fuel injection systems were developed to optimize fuel-air mixture and reduce emissions.
- Catalytic Converters: Improved catalytic converters, often with multiple stages, were employed to effectively convert harmful pollutants into less harmful substances.
- Exhaust Gas Recirculation (EGR): EGR systems recirculate exhaust gases back into the combustion chamber, reducing NOx emissions.
Example: The CB1000 Motor
The SC77 engine, the basis for the new CB1000 motor, was redesigned to meet the stringent Euro 4 standards. This involved incorporating the aforementioned technologies, resulting in significant emissions reductions.
Key Takeaways:
- Euro 4 regulations were a major leap forward in reducing vehicular emissions.
- Engine manufacturers had to implement significant technological advancements to comply.
- The resulting engines, like the CB1000 motor, are cleaner and more efficient.
Euro5 regulations
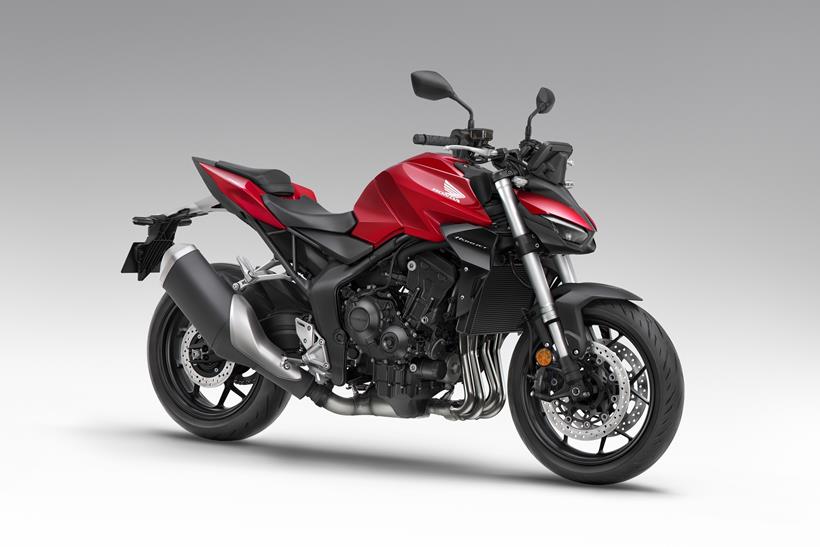
Evolution of Emission Standards: Euro 5 and Euro 5+
The Euro 5 emission standard, implemented in 2020, marked a significant step forward in reducing harmful pollutants from vehicles. It introduced stricter limits for various emissions, including:
- Particulate Matter (PM): Reduced to 0.005 g/km for gasoline vehicles and 0.004 g/km for diesel vehicles.
- Nitrogen Oxides (NOx): Reduced to 60 mg/km for gasoline vehicles and 80 mg/km for diesel vehicles.
Euro 5+ builds upon this foundation with a focus on long-term emission performance. Instead of simply lowering the absolute limits, Euro 5+ emphasizes durability and real-world driving conditions. This means ensuring engines maintain their emissions performance throughout their lifespan, rather than just during initial testing.
Key Takeaways:
- Euro 5+ does not introduce lower absolute emissions limits compared to Euro 5.
- It prioritizes long-term emission control and real-world performance.
Comparison to Earlier Standards:
- Euro 5 standards were a significant step forward from Euro 4, bringing substantial reductions in emissions.
- Euro 5+ further enhances these efforts by focusing on durability and real-world compliance.
Practical Implications:
- Euro 5+ regulations contribute to improved air quality and public health by reducing harmful emissions.
- This standard encourages the development of more advanced engine technologies that are both efficient and environmentally friendly.
Important Notes:
- The Euro 5+ standard focuses on long-term performance and real-world driving conditions, ensuring sustained emissions control throughout the vehicle's life.
- Compliance testing for Euro 5+ is expected to be more stringent, requiring vehicles to demonstrate their emissions performance under various driving scenarios.
- Euro 5+ plays a key role in promoting sustainable mobility and contributing to cleaner air in urban and rural areas.
Euro5+ regulations
Euro5+ Emissions Standards: Beyond the Limit
The Euro5+ emissions standard builds upon the existing Euro5 regulations, introducing a crucial new dimension: durability requirements. While Euro5 established specific limits for pollutants like carbon monoxide (CO), hydrocarbons (HC), and nitrogen oxides (NOx), Euro5+ mandates that these limits must be met for an extended period – 35,000 kilometers (21,748 miles).
This means motorcycles must demonstrate their ability to maintain compliance with the emissions standards throughout their lifespan, not just when they're brand new.
Key Takeaways
- Extended Compliance: Euro5+ enforces a longer period of emissions compliance, ensuring that motorcycles continue to meet environmental standards even after significant mileage.
- Durability Focus: The focus shifts towards ensuring the longevity of emission control systems, leading to potentially more robust and reliable components.
Practical Implications
- Increased Maintenance Costs: To meet the durability requirements, manufacturers may need to incorporate more robust components, potentially leading to slightly higher maintenance costs for consumers.
- Encouraging Innovation: The stricter regulations drive innovation in emission control technologies, leading to potentially more efficient and environmentally friendly motorcycle engines.
- Improved Air Quality: The extended compliance period helps to improve air quality over a longer period, promoting cleaner transportation.
Comparison with Euro5:
While Euro5+ doesn't change the emission limits themselves, it significantly impacts the longevity of those limits. Euro5 focused on initial compliance, whereas Euro5+ ensures that motorcycles continue to meet the standards over a substantial period.
"By extending the compliance period, Euro5+ pushes manufacturers to develop more durable and reliable emission control systems, ultimately contributing to cleaner air and more sustainable transportation."
Engine specifications
Engine Specifications & Performance
The SC77 engine, found in the original Honda Hornet 900, featured a 76mm bore and 55.1mm stroke, resulting in a 919cc displacement. This configuration was considered conservative compared to the high-performance superbikes of its time, and even more so when benchmarked against today's offerings.
- SC77: 76mm bore x 55.1mm stroke, 919cc displacement
- Peak Torque: 86 lb.ft at 11,000 rpm
Comparing to the Modern Hornet
The current Honda Hornet 900 features a more modern engine with a slightly lower peak torque output of 77 lb.ft. However, it achieves this peak at a lower 9,000 rpm. This lower peak torque RPM makes the newer Hornet more usable in real-world riding situations, allowing for smoother acceleration across a broader rev range.
Key Takeaways
- SC77 Engine: A strong, yet relatively conservative engine for its time.
- Modern Hornet Engine: Offers a more practical torque curve for everyday riding.
Practical Implications: The SC77 engine prioritized high-rpm power, delivering a thrilling experience for experienced riders. The newer engine prioritizes everyday usability, making it more accessible to a wider range of riders.
The Honda Fireblade's engine
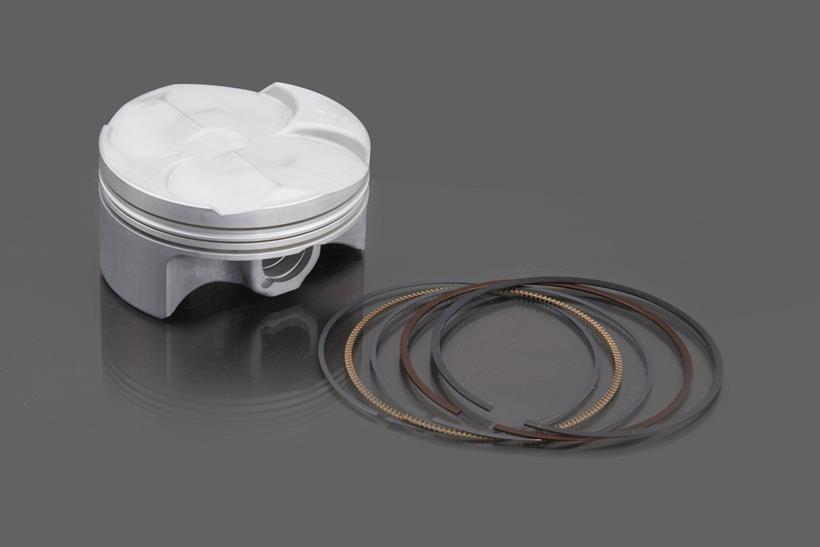
Engine Bore and Stroke: A Balancing Act
The choice of engine bore and stroke, two crucial dimensions in engine design, significantly impacts performance characteristics.
- Bore: The diameter of the cylinder.
- Stroke: The distance the piston travels up and down within the cylinder.
A larger bore generally leads to increased valve area, allowing for greater airflow and higher power output at higher RPMs. This is why Honda's MotoGP bike, the Fireblade, boasts an 81mm bore and 48.5mm stroke, pushing for maximum revs and power.
The Street-Oriented Hornet
However, the Honda Hornet, a street-oriented motorcycle, prioritizes a different set of characteristics. Its design prioritizes:
- Smooth Power Delivery: A shorter stroke and larger bore results in a more balanced power delivery across the rev range, offering a smoother and more enjoyable ride for everyday use.
- Increased Torque: A shorter stroke generally leads to higher torque at lower RPMs, providing better acceleration from a standstill and making the bike easier to ride in city traffic.
Key Takeaways
- Engine Bore & Stroke: These dimensions dictate the engine's characteristics and impact performance in various ways.
- Street-Oriented Bikes: Prioritize smooth power delivery and torque for a more comfortable ride in everyday scenarios.
- Sport Bikes: Often favor high-revving engines with large bore and short stroke for maximum power output.
Practical Implications:
Choosing the right bore and stroke for a motorcycle depends on its intended use. Street bikes often prioritize smoothness and torque for everyday riding, while sport bikes prioritize high-revving power for track performance. This fundamental design consideration dictates the very nature of the motorcycle and its appeal to its target audience.
Engine modifications for the CB1000 Hornet
Reducing Engine Revs for Improved Performance and Efficiency
Key Takeaway: Reducing engine revs can significantly improve fuel economy, reduce emissions, and enhance engine longevity, particularly crucial for meeting stringent Euro5+ standards.
Honda's Hornet motorcycle exemplifies this principle by incorporating smaller throttle bodies, decreasing from 48mm to 44mm. This seemingly subtle change has a profound impact on engine behavior:
Increased Intake Velocity & Torque Enhancement
- Smaller throttle bodies: By reducing the throttle body diameter, the air flow velocity entering the engine increases.
- Enhanced midrange torque: This increased velocity results in improved combustion efficiency and a boost in torque, particularly in the midrange RPM range.
- Practical Implications: This translates to a more responsive and enjoyable riding experience, with improved acceleration across a wider RPM band.
Technical Specifications
- Throttle body diameter: 44mm (Hornet) vs. 48mm (predecessor)
- Intake velocity: Higher in the Hornet due to the smaller throttle body.
- Torque output: Increased in the midrange RPMs for improved acceleration.
Comparison with Traditional Methods
- Conventional approach: Larger throttle bodies are often used to increase airflow, but this can lead to reduced fuel efficiency and increased emissions.
- Honda's approach: Smaller throttle bodies, coupled with optimized intake design, improve efficiency and performance.
Important Note: This strategy of reducing revs for efficiency is gaining traction across various engine applications, particularly in the automotive industry. It is a testament to Honda's commitment to innovation and environmental responsibility.
More engine modifications
Engine Modification for Improved Combustion Control
Honda's recent engine revisions are aimed at mitigating the risk of pre-ignition, a common issue in high-performance engines.
Reduced Valve Lift and Timing
- Reduced valve lift: This decreases the amount of air entering the cylinder during the intake stroke, resulting in a lower volumetric efficiency.
- Revised timing: This alters the timing of the valve events (intake and exhaust), influencing the air-fuel mixture within the cylinder.
These modifications, when combined, lead to a less aggressive combustion process, reducing the likelihood of pre-ignition.
Lower Compression Ratio
- Compression ratio: This is the ratio of the volume of the cylinder when the piston is at the bottom of its stroke to the volume when it is at the top.
- Honda's revised CR: From 13:1 to 11.7:1.
This reduction in compression ratio significantly lowers the peak combustion temperature, further reducing the risks of pre-ignition.
Key Takeaways
- The combination of reduced valve lift, revised timing, and lower compression ratio effectively reduces the likelihood of pre-ignition.
- Lowering combustion temperatures is crucial for preventing pre-ignition, a condition that can lead to engine damage.
Practical Implications
These modifications, while contributing to improved combustion control, can have performance trade-offs. The reduction in valve lift and compression ratio can lead to a slight decrease in power output. However, the benefits in terms of engine reliability and longevity outweigh these potential drawbacks.
Comparison to Other Technologies
This approach to pre-ignition mitigation is commonly seen in high-performance engines. Other methods include:
- Advanced ignition systems: These systems adjust the timing of the spark plug firing to optimize combustion.
- Water-injection systems: These inject water into the intake manifold to lower combustion temperatures.
- Variable valve lift systems: These systems adjust the valve lift dynamically, allowing for optimal combustion at different engine speeds and loads.
Results of the modifications
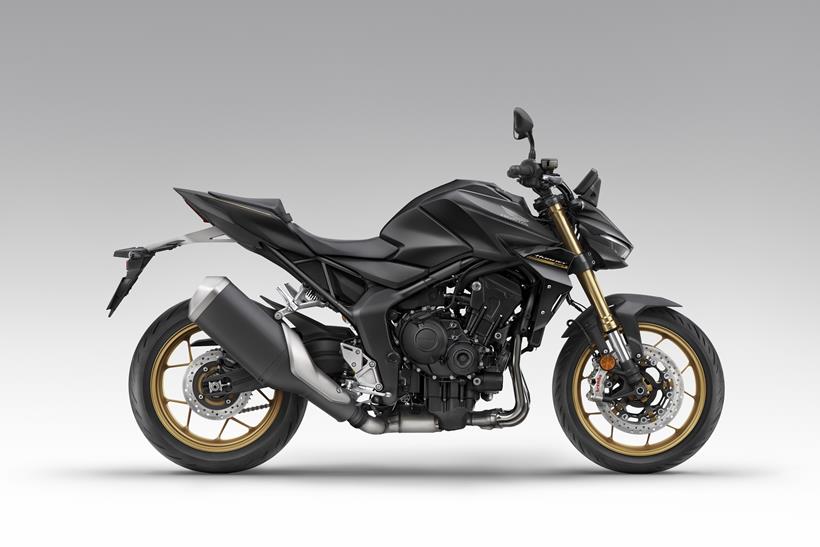
Engine Tuning for Enhanced Durability and Cost Savings
The Hornet's engine boasts a revised powerband compared to its predecessor, the Blade. Peak power is achieved at 11,000 rpm, down from 13,000 rpm in the Blade, while maximum torque is reached at 9,000 rpm instead of 11,000 rpm.
Technical Specifications
- Peak Power: 11,000 rpm (Hornet) vs 13,000 rpm (Blade)
- Max Torque: 9,000 rpm (Hornet) vs 11,000 rpm (Blade)
Key Takeaways
- Lower RPM: The lower peak power and torque RPMs in the Hornet translate to less stress on the engine components, leading to enhanced durability and longevity.
- Cost Savings: Reduced stress allows for the use of less expensive materials in the engine construction.
Material Choices
- Inlet Valves: The Hornet utilizes steel inlet valves, while the Blade employed titanium valves. Steel is a less expensive and heavier material, but it offers sufficient durability at the lower operating RPMs of the Hornet.
- Engine Covers: The Hornet features aluminum engine covers, whereas the Blade used magnesium covers. Aluminum is more affordable than magnesium and offers comparable performance in this context.
Practical Implications
The shift to lower engine RPMs and the use of less expensive materials contribute to an overall cost reduction in the Hornet's production, making it more accessible to a wider range of riders without compromising on reliability and performance.
Comparison with Similar Technologies
This approach aligns with the design philosophy adopted by many modern motorcycle manufacturers, where prioritizing durability and affordability often takes precedence over achieving extremely high RPM limits.
The CB1000 Hornet's performance
Honda Hornet: Power and Performance
The Honda Hornet, while offering a respectable power output, does fall short of its predecessor, the Fireblade, in terms of peak power and torque.
Power and Torque Figures
- Hornet: 149.7 bhp
- Fireblade: (Specify the Fireblade's power output for comparison)
Important Notes:
- While the Hornet's power figures may be lower, it still delivers a thrilling ride and remains competitive within its class.
- The Hornet's performance is likely to be influenced by its weight (specify weight if available) and engine size (specify engine size) compared to the Fireblade.
Practical Implications
The Hornet's power output makes it a versatile motorcycle suitable for:
- Everyday commuting: The engine's responsive nature makes navigating city traffic a breeze.
- Weekend rides: The Hornet is capable of spirited rides on winding roads, offering a balance of performance and handling.
- Track days: While not a full-fledged race bike, the Hornet can be a fun and capable machine on the track.
Key Takeaways:
- The Hornet's power output is a trade-off for its overall weight and design, prioritizing everyday usability.
- The Hornet's lower power figures do not detract from its overall riding experience, as it still delivers a thrilling and engaging ride.
The benefits of repurposing the Fireblade engine
Repurposing Technology: A Win for Customers
Repurposing the Blade engine for the new Hornet offers significant advantages, particularly for customers.
Cost Savings through Reduced R&D and Tooling
- Reduced R&D Costs: By leveraging the existing design and development work invested in the Blade engine, Hornet's R&D costs are significantly lower. This translates to a more efficient development process and faster time to market.
- Reduced Tooling Costs: The existing production tooling for the Blade engine can be reused for the Hornet, minimizing the need for new tooling investments. This further reduces manufacturing costs.
Practical Implications for Customers
These cost savings are directly passed on to customers in the form of a lower price tag for the Hornet. This makes the Hornet a more attractive option for budget-conscious buyers.
Important Notes
- Repurposing an existing engine design can also expedite the development process, allowing for a quicker launch of the Hornet.
- This approach also minimizes the risk associated with developing a completely new engine.
Real-World Applications: This strategy is common in various industries, from automotive to aerospace. For example, automakers often repurpose existing platforms and components for new models to reduce development time and costs.